Let Them Screen Prints!: Production for the Masses
By: Rachel T, rachel.t@annarbortees.com
almost 8 years
As we discussed in our previous post, For Their Dyes Only: the Secret of Silk, printing in its early forms had been around for hundreds of years. However, the scientific and technological advances of the industrial revolution reinvented the practice. Screen printing began to focus on streamlined mass production as opposed to the painstaking craft of yore. Some of the earliest machine printing with stencils started during the late 1880's.
How did printers copy an image?
At that time, both the US and the UK created their own processes, known respectively as Mimeograph and Cyclostyle. Both countries used machines with handcrafted stencils on waxed mulberry paper. The same mulberry trees the silkworms eat actually made up the paper. The paper stencils were then fastened onto the ink-filled drum of a rotary machine. By turning a crank, a piece of paper would feed through the machine while the ink-filled drum turned. A crude squeegee would press ink through the mesh of the drum and print the image from the stencil.
What was the downside?
The handmade stencils, although a breakthrough in the craft of printing, were quite fragile. Also, letters and designs that had free-floating centers needed to be connected or “tied” to the stencil. Otherwise, the design would lose that detail. For example, the middle of the letter “O” would fall off without any ties and a filled in circle would result. Although they changed the physical look of letters some, ties kept the end result recognizable. Size was also a major concern because if the details were too small, the stencil would be too fragile to support itself. As a result, the handmade stencils limited artists to large designs and fonts that could support the detail.
Stencils, Substrates, and Silk Screens!
Screen printing soon incorporated many of these new ideas into its’ own process. In 1907, Samuel Simon of Manchester England gained a patent for using silk to support a stencil. He used a brush to press the paint through the silk mesh and onto the substrate (anything one prints on). At the time, silkscreening was mainly used on wallpaper and linen. In 1920, Albert Kosloff gave a demonstration printing ink through a screen using a squeegee. The squeegees soon replaced brushes. Printers still use squeegees today either drawn across a screen manually or clamped into an automated press.
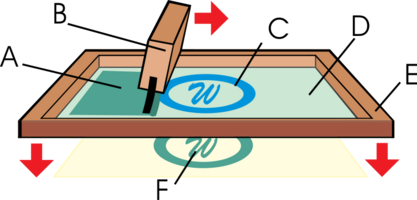
A. Ink B. Squeegee C. Image D. Silk Screen E. Screen Frame F. Printed Image - Image by Harry Wad
More advances in screen printing were soon to come. Read on to our next blog, Ready for the Closeup: Photographic Screens, to learn how the invention of photographic screens allowed for more detailed prints.
Request Pricing
References
- http://www.ooshirts.com/guides/History-of-Screen-Printing.html
- http://www.visual-arts-cork.com/prehistoric/hand-stencils-rock-art.htm
- http://www.brighthub.com/multimedia/publishing/articles/105324.aspx
- http://revolverwarholgallery.com/andy-warhol-screenprints-process-history/
- https://www.dfcscreenprinting.com/blog/the-history-of-silk-screen-printing.html
- http://www.visual-arts-cork.com/printmaking/screen-printing.htm
- https://en.wikipedia.org/wiki/Silk
- https://en.wikipedia.org/wiki/Screen_printing
- http://www.gwent.org/gem_screen_printing.html#history
- Book - Mental Floss History of the World
- https://en.wikipedia.org/wiki/Mimeograph
- http://homepage.usask.ca/~nis715/scrnprnt.html
Tags: #screen printing, #learn about printing, #history